Glycerol is a low-value byproduct from bio-diesel production. A new process patented by DTU Chemistry can convert glycerol into the monomer allyl alcohol which can be polymerized into plastic.
Production of bio-diesel by trans-esterification of sorted household garbage and waste from the meat industry is already a large step forward for sustainability. However, trans-esterification also yields about 10% glycerol. Presently bio-diesel producers can sell this byproduct at symbolic prices only – hardly covering the cost of capturing and purifying the glycerol. Now, researchers at DTU Chemistry has found a feasible route for turning glycerol into allyl alcohol. Allyl alcohol is a valuable raw product in the fine chemicals industry, where this monomer – normally produced from crude oil – is polymerized into a range of polymers.
“A catalytic route was identified about five years ago, but that was relying on the rare and expensive element Rhenium as catalyst. We have shown that the same result can be achieved using Molybdenum instead. Since the cost of Rhenium is about 100 times higher than the cost of Molybdenum, this is a significant step towards a process which can be implemented by industry,” says Associate Professor Peter Fristrup, DTU Chemistry. “A further practical advantage of the new process is that it will be pretty straightforward to add to the existing glycerol purfication process.”
Zero is left for the landfill
The plant operated by Daka near Horsens produces about 5,000 tons of glycerol annually as a byproduct from bio-diesel production. The process developed by Peter Fristrup’s group will be able to convert at least 25% of the glycerol into allyl alcohol.
Allyl alcohol can be converted into a wide range of chemical building blocks – for example into acrylic acid which can be polymerized to give the super-absorbent polymer known from diapers.
“The remaining fraction can be processed further, and the end product here is a dark, robust substance which can be burned - so at least you will get energy from it. One of the possible solutions for the surplus of glycerol is to burn it – but glycerol burns notoriously badly. Our technology actually solves this problem by generating a much more easily flammable product through water removal. In this way the entire raw material will have been used, leaving nothing to be deposited at a landfill,” says Peter Fristrup. “This will be a fine example of the circular economy where byproducts are seen as a resource rather than waste.”
DTU Chemistry is currently discussing further cooperation with Daka as well as other partners interested in 100% bio-based allyl alcohol, acrylic acid or 1,4-butane diol.
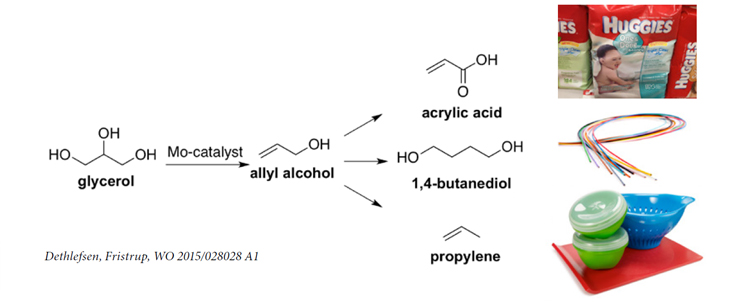
More economic than fermentation
The group has filed several patents concerning the Molybdenum-catalyzed process and similar processes for biomass conversion.
A different application is being pursued in collaboration with industry partner Haldor Topsoe as part of the national BIOVALUE-initiative (total budget DKr. 170 mio.). Specialized in catalysis the company has developed several catalysts for production of lactic acid from sugar.
“I cannot reveal the details yet, but in general terms I can say that the perspective is that Topsoe is able to obtain other products than lactic acid using the same catalysts. These products may be processed into new bio-based polymers – hopefully in a more efficient way than alternative routes – or they may find completely new applications,” states Peter Fristrup.
Lactic acid can be polymerized into PLA, Poly Lactic Acid. PLA has several applications. One example is as a benign matrix for 3D printers, another one is for bio-degradable disposable cups and plates.
“I would like to stress that one should not always assume that products originating from biomass sources are more biodegradable than similar products from crude oil. This is a widespread misunderstanding. However, in the case of PLA the biodegradability is actually very good, making this polymer highly suitable for disposable products.”
Lactic acid is traditionally produced by fermentation. The Topsoe process are more direct, chemical routes to the end product. Unlike fermentation they do not involve tanks with water and microorganisms and thus avoids amounts of slurry which needs to be treated afterwards. Further, the catalytic processes can run at elevated temperatures, since no microorganisms need to be nursed, which will speed up processes and improve economy.
Mimicking oil formation
Besides patent applications, the group has a steady production of scientific articles. Peter Fristrup is confident that this situation will continue despite an overall backlash for bio-plastics:
“The price of crude oil is currently very low. This has made it harder for companies to create good business cases for bio-plastics. Still, it is beyond doubt that bio-plastics will play a major role in the future. After all, crude oil is a non-renewable source with high CO2 burden, while straw, food waste and a number of other bio-materials are renewable, cheap, and CO2 neutral raw materials. In one case we can even incorporate CO2 into the product and if surplus electricity from wind power is used this could potentially make the bio-plastic CO2 negative!”
Research at DTU Chemistry has shown that a number of products produced from crude oil today can also be produced from biomass, he notes: “As chemists we are extremely proud of these achievements. One prominent challenge is the fact that biomass has a much higher oxygen content than crude oil. Removing this oxygen is tricky, since the processes needed typically have very high activation energies – meaning they would not occur spontaneously or only very slow in nature. In fact, nature has spent millions of years removing this oxygen under the extreme conditions which prevail in the crude oil reservoirs. We are now able to mimic these processes in our laboratories – only at much, much higher rates. It may well be that these processes are not in high demand just now, because we cannot compete with the current low prices for crude oil, but I am confident that they will find applications. This could either be in contexts where a higher price is acceptable due to the better climate protection properties of biomassderived products, or it could be because different products are accessible such as for example PLA which cannot be produced from crude oil.”
Until the end of 2015, the research described in the article was mainly financed by a Sapere Aude Research Leader Award obtained by Peter Fristrup from the Danish Council for Independent Research and has resulted in 3 patent applications and more than 10 research publications. The activities with Haldor Topsoe continue under a new grant from the Danish Innovation Fund. Professor Robert Madsen coordinates DTU Chemistry participation in the new project, which also involves industry partners Haldor Topsoe (Denmark) and Perstorp (Sweden).